减量发展
进入21世纪以来,亚洲地区生铁产量增长尤为突出,中国、印度和韩国等生铁产量的增长引领全球生铁产量的增长。“十五”和“十一五”时期,炼铁产量进入两位数的高速增长时期,进入“十二五”时期,炼铁产量增速趋缓,但仍保持个位数的增速。与此同时,中国生铁产量占世界生铁产量的比重趋于增加和稳定,已超过半壁江山,而过高的生铁产量给削减CO2和环保(SO2、烟粉尘排放等)带来较大的压力。铁产量增长率逐年波动下行,是由经济发展的客观规律所决定的,炼铁业进入增速换挡期;炼铁进入减量化发展阶段,是加快经济发展方式转变的主动选择,炼铁业进入结构调整阵痛期;降产量、去产能,是化解多年来积累的深层次矛盾的必经阶段,炼铁业进入前期刺激政策消化期。在三期叠加过程中,炼铁业机遇和挑战并存,矛盾和风险凸显,须转变发展理念。炼铁业认识、适应、把握和引领新常态,是“十三五”时期炼铁发展的大逻辑。
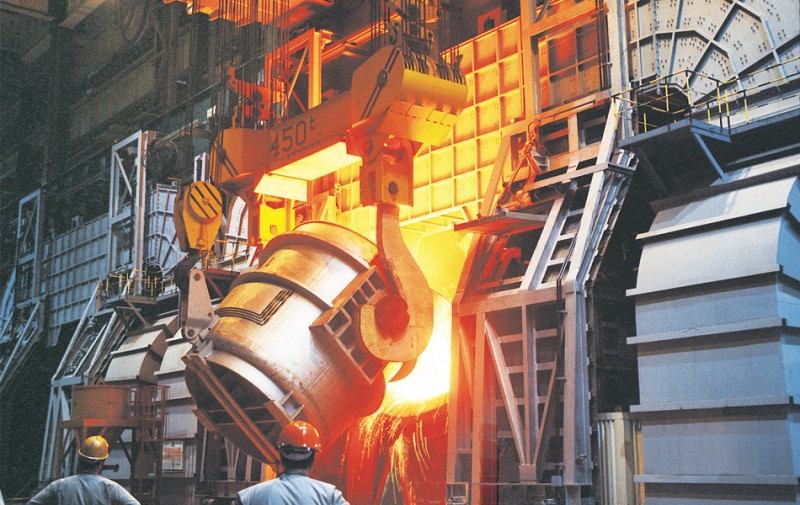
降本增效
在产能严重过剩、产品同质化竞争严重的环境中,成本竞争力逐渐成为核心竞争力。生铁成本低则竞争力强,有利润就能发展,反之亏损就会被市场淘汰。钢铁企业的总成本可分为制造成本、管理费用、财务费用、销售费用4个部分,其中制造成本约占总成本的65%左右,而制造成本中约有70%属于铁前工序。从近期看,成本高低与工艺、技术和管理水平等有关,这是可改变的竞争因素。通过生铁对标挖潜分析可发现企业的潜力,促进企业通过技术进步和改善管理达到降低成本的目的。铁前系统的对标挖潜、降本增效,应围绕以下8个方面进行优化:
优化焦化配煤结构。通过优化配煤结构,提高焦炭质量,增加低成本弱黏结煤、进口主焦煤等煤种的配比,达到合理利用炼焦煤资源、降低成本的目的;
优化烧结混匀料配比。通过优化配比,提高烧结矿质量,合理利用两种矿石资源,充分利用各种含铁废料,提高烧结矿性价比。烧结优化配矿以铁矿粉高温烧结基础特性(同化性、液相流动性、铁酸钙生产能力等)为约束条件,综合考虑化学成分等,采用基于铁水成本最低的烧结优化配料模型;
优化球团矿配比。通过优化配比,合理利用精矿粉资源,提高球团矿质量,提高球团矿性价比;
优化高炉入炉原料结构。通过优化炉料结构,奠定高炉长期稳定顺行的基础,实现高效、低碳、低成本的冶炼效果。以铁水成本最低为目标,建立高炉配料优化数学模型,实现铁水成本最低的优化配料;
优化高炉燃料结构。选择合理的入炉焦炭粒度,提高冶金焦率,充分利用焦炭资源;选择适宜的喷煤量,实现最适宜的燃料比与经济效果;优化喷吹煤结构,提高性价比高的喷吹煤比例,确定最佳的烟煤、无烟煤混合比例,提高煤焦置换比;
优化原燃料采购结构。延伸铁前系统优化工作,把原燃料结构优化延伸到采购环节,以原燃料结构优化的结果指导采购,使采购的性价比高的原燃料品种满足结构优化的需求,实现采购与结构优化的有机结合;
优化物流。优化运输方式,提高低运价模式的比例;优化运输路线,缩短运输距离;优化进口料到港,为优化运输创造条件;优化库存管理,保持合理库存,减少厂内倒运和转运;
优化二次能源利用。完善烧结、炼铁工序等余压、余热、余能的回收利用设施,实现二次能源的充分利用;优化设备运行方式,提高能源转换效率;实现煤气平衡规划,提高富余煤浪费。
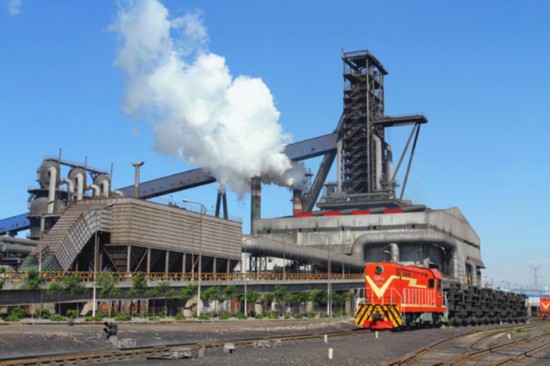
技术创新
“十三五”时期,炼铁技术应在如下几个方面进行转型升级和创新发展:
烧结烟气循环利用工艺。烧结烟气循环利用技术将收集全部或部分风箱的烟气,循环返回到烧结料层。废气中的有害成分将在进入烧结层后被热分解或转化,二英和NOX会被部分消除,抑制NOX的生成;粉尘和SOX会被烧结层捕获,减少粉尘、SOX的排放量;烟气中的CO作为燃料使用,可降低固体燃耗。另外,烟气循环利用减少了烟囱处排放的烟气量,减轻了终端处理的负荷,可提高烧结烟气中的SO2浓度和脱硫装置的脱硫效率,降低脱硫装置的规格,减少脱硫装置的投资。
该工艺已有不同的流程,在欧洲、日本和中国等钢厂应用。生产实践应用表明,烧结烟气循环技术可减少烧结烟气的外排总量,是减轻烧结厂烟气污染的最有效手段;可大幅降低烧结厂烟气处理设施的投资和运行费用;可减少外排烟气带走的热量,减少热损失,实现CO二次燃烧,降低固体燃耗;可减少外排烟气中的有害物质总量。欧洲某些烧结厂甚至用此工艺而未上烟气末端处理系统。
经过不断创新和发展,国内外目前主要有5种烟气循环利用的工业化烧结技术方案:EOS、LEEP、EPOSINT、区域性废气循环和烧结废气余热循环技术。烟气循环烧结工艺可使烧结生产的各种污染物排放量减少45~80%,固体燃耗降低2~5kg/t或工序能耗降低5%以上。
烧结竖罐冷却和余热发电技术。竖冷窑冷却热烧结矿及余热回收技术装置可替代烧结机环冷机、带冷机作为新建项目的烧结工艺冷却设备,也可替代既有烧结的环冷机、带冷机,实现热烧结矿显热的高效回收。特别是对于既有的步进式烧结机,采用竖冷窑替代机上冷却功能,将原机上冷却段改为烧结段以加大烧结面积,使原烧结机产量提高约70%,同时烧结矿显热可实现高效极限回收。
采用竖罐冷却技术代替环冷机或带冷机,冷却风供风总量可减少一半左右;热烟气100%全部回收,且温度约可提高至450℃以上,余热回收效率显著提高;与环冷机余热回收总量相比,约可提高60~80%,增效明显。
含镁或熔剂性球团矿生产和应用。首钢京唐公司球团厂2012年6月组织配加MgO球团的工业试验表明,配加MgO粉能改善球团矿冶金性能,降低其还原膨胀率。凌源钢铁公司、津西钢铁公司等曾采用熔剂性球团替代酸性球团冶炼,取得焦比降低、利用系数提高的效果。曹妃甸带式焙烧机和湛江龙腾球团设计有MgO配加装置,具备生产含MgO或熔剂性球团的条件。
高炉冲渣水余热回收或余热发电。冲渣水余热的回收方式主要包括利用冲渣水采暖、用于浴池用水和利用余热发电。北方地区部分钢厂利用冲渣水采暖、用于浴池用水,或用于钢铁企业的鼓风预热、除盐水预热、混料加热、设备的除湿热水等供应,并给钢企带来可观的经济效益。
该技术在钢铁企业推广,可减轻钢企节能减排的压力,增加钢企非钢产业的收入。高炉冲渣水余热回收利用的回收期短,经济效益显著,为钢厂发展非钢产业提供了新的途径。
高炉冲渣水替换燃煤锅炉采暖,彻底解决了燃煤锅炉外排废气、SO2等污染物的问题,从源头上减少甚至消除雾霾的发生。同时,该技术不需要购买燃气、不需要储存燃煤的仓库,以及取消运输燃煤的物流环节,使人力、物力成本也大大降低,给城市运转减少压力,并有效解决长期困扰城市的供暖资金短缺问题。南方地区开发低温余热资源最成熟的技术———有机朗肯低温余热发电技术(ORC),将高炉冲渣水余热回收用于低温余热发电,其市场前景广阔。
该技术为城市与钢铁企业融合发展提供了新途径,为城市型钢铁企业的融合发展提供了新模式,为加速城市型钢厂绿色转型、融入城市经济圈提供了重要支撑。
高炉煤气提纯技术创新。高炉煤气提纯(或浓缩)是采用变压吸附(VPSA)方式,将高炉煤气中的主要可燃气体CO进行提纯(或浓缩),根据用户需求得到含40~99.99%CO的产品气。该产品气可作为高热值燃烧气体(燃料)、高炉还原性气体,还可用于生产化工产品如合成氨、甲醇、醋酸和二甲醚等。对于存在高炉煤气富余或煤气放散现象严重的钢铁企业,可将富余高炉煤气通过变压吸附提纯后进行高炉炉顶煤气循环,用于高炉喷吹,可大幅度降低入炉焦比,实现低碳炼铁和节能减排。也可将高炉煤气提纯得到的含70%左右CO的气体替代天然气、液化气使用,缓解煤气资源紧张,用于轧钢加热炉或退火炉,减少外购天然气,降低企业生产成本。该技术已在国内某钢厂成功投运。FINEX炉顶煤气经变压吸附提纯后循环使用,燃料比(煤比)下降明显,实现了低碳炼铁、节能减排,降低了生产成本。
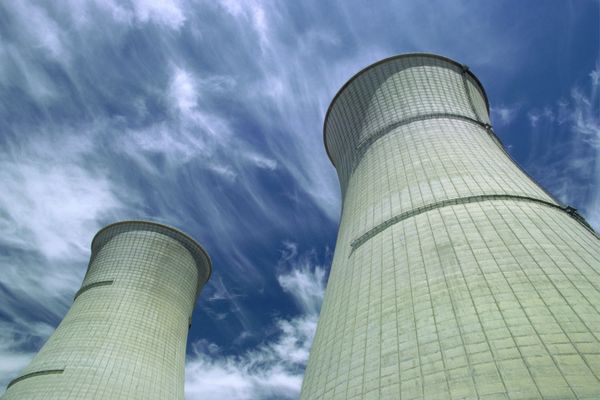
风险管控
“十三五”期间,炼铁业在去产能任务紧迫、微利或亏损经营、环保压力大、资金链紧张等背景下,风险日益加大,高炉生产亟待由追求产量向低成本生产转变。由于资金链紧张甚至断裂,高炉被迫减产或停炉;由于耐材质量和操作管理等方面的因素,炉缸烧穿、煤气泄漏、爆炸或高温烧伤等安全事故多发;由于环保达标改造和核查,高炉生产面临非计划休风等……炼铁工作者要兼顾合理组织、安全生产和高炉长寿的关系,做好生产、技术、成本和效益方面的平衡,做好风险预案和风险管控工作,以减少不必要的损失。
综上所述,“十三五”期间,炼铁业应认识新常态、适应新常态、把握新常态和引领新常态,通过减量发展、降本增效、技术创新、风险管控等途径,实现炼铁转型升级和创新发展。技术创新的方向主要包括:烧结烟气循环工艺、烧结竖罐冷却和余热发电技术、含镁或熔剂性球团生产和应用、高炉冲渣水余热回收利用技术、高炉煤气提纯技术等。